گروهی از محققان دانشگاه صنعتی کاوناس (KTU) و موسسه انرژی لیتوانی روشی برای بازیافت پرههای توربین بادی پیشنهاد کردند. آنها با استفاده از تجزیه در اثر حرارت، مواد کامپوزیتی را به اجزای تشکیل دهنده خود، یعنی فنل و فیبر، شکستند. به گفته دانشمندان، مواد استخراج شده قابل استفاده مجدد هستند و این فرآیند عملاً بدون زباله است.
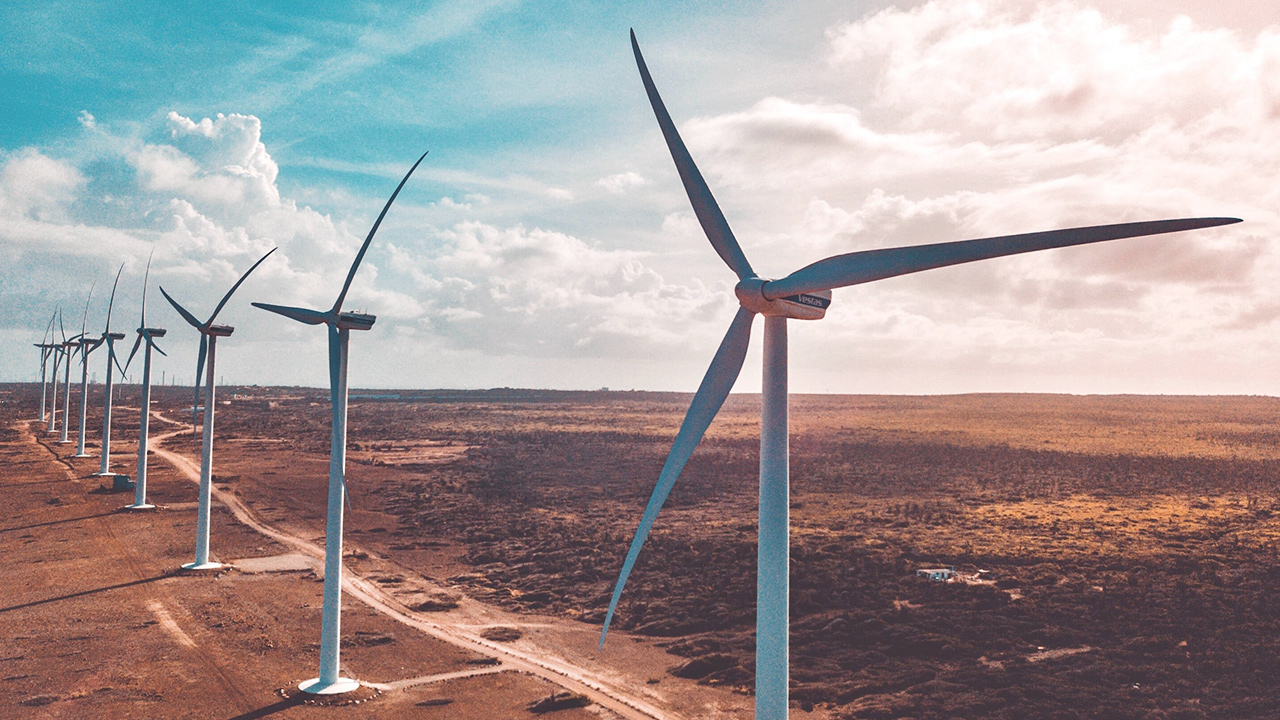
نانوذرات بازدهی فرآیند بازیافت پرههای توربین بادی را افزایش میدهند
پرههای توربین بادی ساخته شده از کامپوزیتهای ورقهای پلیمری تقویت شده با الیاف شیشه (GFRP) میتوانند تا ۲۵ سال کار کنند. پس از آن، این پرهها در محلهای دفن زباله قرار می گیرند. از آنجایی که کامپوزیتهای GFRP به عنوان مواد بسیار مقاوم در برابر تجزیه و شکستن شناخته میشود، مسئله دفع زبالههای این پرهها به یک چالش واقعی برای صنعت انرژیهای تجدیدپذیر تبدیل شده است.
تخمین زده می شود که پره های توربین بادی ۱۰ درصد ضایعات مواد کامپوزیتی تقویت شده با فیبر را در اروپا تشکیل میدهند. محققان ادعا میکنند که تا سال ۲۰۵۰، ضایعات پرههای توربین بادی به حدود دو میلیون تن در سطح جهان افزایش خواهد یافت. از آنجایی که بسیاری از کشورها دفن مواد کامپوزیتی را در محلهای دفن زباله خود ممنوع کردهاند، بازیافت پرههای استفاده شده توربین بادی به چالشی تبدیل میشود که محققان در سراسر جهان در تلاش برای حل آن هستند.
سامی یوسف، محقق دانشگاه صنعتی کاوناس (KTU)، میگوید: «چندین سال پیش موضوع کاهش انتشار گازهای گلخانهای جهانی تا سال ۲۰۵۰ به نزدیک به صفر، مطرح شد. از آن زمان، کشورهای بیشتری با سرمایهگذاری در منابع انرژی تجدیدپذیر، از جمله انرژی باد، به هدف خالص صفر متعهد شدهاند. با این حال، بازیافت پرههای توربین بادی که به اندازه یک زمین فوتبال بوده، بسیار محکم و دارای پلاستیک هستند، مشکل جدی است. بدون راهحلی امکانپذیر برای آن، نمیتوان گفت که انرژی باد کاملاً پایدار و سازگار با محیطزیست است.
با هدف مقابله با این چالش، این گروه تحقیقاتی به سرپرستی دکتر یوسف چندین آزمایش را انجام داده اند که شامل تجزیه GFRP به اجزای تشکیلدهنده آن است.
کامپوزیتهای GFRP به دلیل استحکام، سادگی شکلدهی و هزینههای ساخت کم، برای اهداف متعددی نظیر ساخت خودرو، کشتیهای دریایی، تولید نفت و گاز، ساختوساز، کالاهای ورزشی و موارد دیگر استفاده میشوند. هواپیما، انرژی بادی و الکترونیک از جمله صنایعی هستند که بیشترین استفاده را از GFRP دارند و تقاضای جهانی سالانه ۶ درصد افزایش مییابد.
سامی یوسف میگوید: «کامپوزیتهای GFRP که برای بسیاری از صنایع از جمله تولید پرههای توربینهای بادی استفاده میشوند، ترموست یا ترموپلاستیک هستند. این کامپوزیتها از دو جزء تشکیل شدهاند، فیبر و رزین. در مورد الیاف، معمولاً از جنس فیبر کربن یا فایبرگلاس است (دومی ارزانتر است).»
در این پروژه، محققان اقدام به اعمال پیرولیز (در حضور کاتالیزور زئولیت و بدون کاتالیست) به دستههای مختلف کامپوزیت – ترموست فایبرگلاس و ترموپلاستیک فایبر گلاس – میزان استخراج فنل (جزء اصلی در تولید رزینهای فنلی) را اندازهگیری کردند. نتایج یافتههای آنها نشان داد که افزودن نانوذرات میتواند کارایی این فرآیند را بهبود دهد.
اگرچه بازده اجزای استخراج شده در طی پیرولیز بسته به دماهای اعمال شده متفاوت است، اندازهگیری تقریبی نشان داد که در همه موارد، ترکیبات فرار متعدد (تا ۶۶ درصد) و باقی مانده فیبر (حدود ۳۰ درصد) استخراج شدهاند. این یافتهها نشان داد که نانوذرات اضافه شده (نانولولههای کربنی و گرافن) باعث افزایش بازده فنل شد.
اجزای فرار اساساً فنل هستند که میتوانند برای تولید بیشتر رزین مورد استفاده قرار گیرند و باقیمانده الیاف پس از تصفیه شیمیایی آن میتواند کاربردهای متعددی نظیر بتن تقویت شده با الیاف، کامپوزیتهای پلیمری، کفپوش الیافی داشته باشد. یوسف میگوید روش ما تقریباً بدون ضایعات با انتشار کمی است.
در حال حاضر، این گروه تحقیقاتی در حال ایجاد مدلی است که به مقیاس و محاسبه اثرات اقتصادی و زیست محیطی گستردهتر نتایج میپردازد.