پژوهشگران دانشکده مهندسی مواد دانشگاه صنعتی مالک اشتر با طراحی و بهینه سازی پارامترهای مختلف پاششهای نانوساختار توانستند به پوششی با کیفیت بسیار مطلوب دست پیدا کنند و مشکلات اصلی پاشش و چسبندگی پوششهای سد حرارتی نانوساختار به زیر لایه را برطرف کنند.
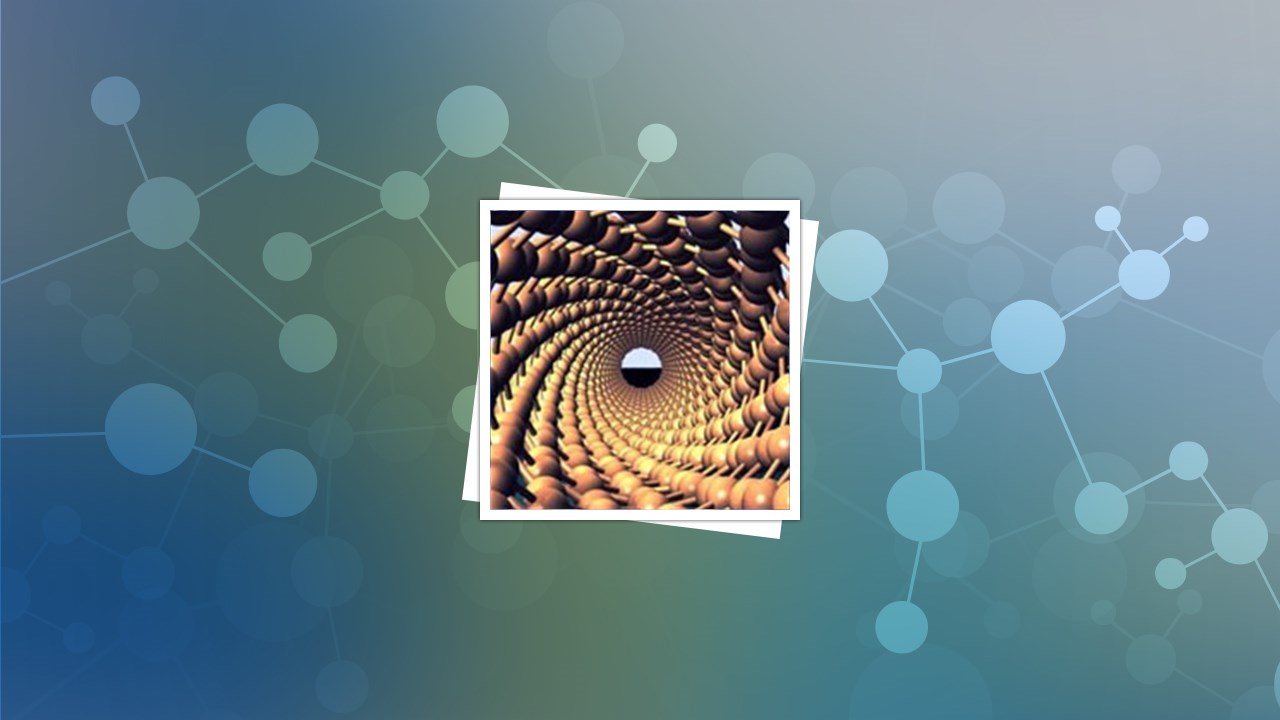
رفع مشکلات اصلی پوششهای سد حرارتی نانوساختار با پاشش کنترل شده
پژوهشگران دانشکده مهندسی مواد دانشگاه صنعتی مالک اشتر با طراحی و بهینه سازی پارامترهای مختلف پاششهای نانوساختار توانستند به پوششی با کیفیت بسیار مطلوب دست پیدا کنند و مشکلات اصلی پاشش و چسبندگی پوششهای سد حرارتی نانوساختار به زیر لایه را برطرف کنند. کاربرد این طرح در صنایع هوافضا، نیروگاهی، نفت وگاز، خودروسازی شامل توربینهای بخار، مبدلهای حرارتی، بویلرها، توربینهای گازی، موتور هواپیما و جهت پوششدهی تمامی قطعاتی که در دماهای بالا کار میکنند، است.
پوششهای سد حرارتی نقش مهمی در حفاظت اجزای قسمتهایی که در دمای بالا قرار دارند، ایفا میکنند. با استفاده از این
پوششها، به علت هدایت حرارتی بسیار کم و قابلیت تحمل شیبهای حرارتی، امکان افزایش دمای کاری توربین و به دنبال آن بازده ترمودینامیکی، بهبود و انتشار آلایندهها کاهش مییابد. با وجود آنکه تعداد و اهمیت کاربردهای پوششهای سد حرارتی به طور گستردهای گسترش یافته است اما هنوز، انهدام زود هنگام ناشی از پوسته شدن پوششهای سد حرارتی حین کارکرد، که میتواند فلز بدون پوشش را به طور خطرناکی در معرض گازهای داغ قرار دهد، از اهمیت خاصی برخوردار است. در نتیجه مطالعاتی در مورد پوششهای سد حرارتی بر روی بهبود خواص مکانیکی، مقاومت به خوردگی، اکسیداسیون و مقاومت به شوک حرارتی، به منظور افزایش عمر کاری و قابلیت اطمینانپذیری پوششهای سد حرارتی در دماهای بالاتر متمرکز شد. استفاده از پوششهای زیرکنیایی نانوساختار را میتوان یک روش بهینهسازی کاربردی پوششهای عایق حرارتی دانست. امروزه تولید پوششهای نانوساختار زمینه جدیدی را در صنعت پاشش حرارتی ایجاد کرده است به طوریکه توسعهی پوششهای نانوساختار YSZ میتواند باعث بهبود کارایی پوششهای سد حرارتی، به دلیل ضریب هدایت حرارتی کم، ضریب انبساط حرارتی بالا و خواص مکانیکی عالی این نوع پوششها شود.
ریزساختار پوششهای نانوساختار پاشش پلاسمایی شده، از ذرات پودری ذوب نشده یا نیمهمذاب پراکنده شده در سرتاسر پوشش، که به وسیله بخش حاصل از انجماد ذرات کاملا مذاب احاطه شدهاند، تشکیل میشود. بنابراین، در طی پاشش ذرات پودری نانوساختار، اجتناب از ذوب کامل ماده به منظور حفظ بخشی از ساختار نانو در ریزساختار پوشش، امری ضروری است. به هر حال، به منظور حصول شرایط فیزیکی لازم برای چسبندگی و همچسبی ذرهای، درجهای از ذوب ضروری است. این امر یک چالش برای پاشش حرارتی پودرهای نانوساختار است؛ چنانچه تمام ذرات پودری به صورت کامل در جت پلاسما ذوب شوند، ساختار نانومتری پودر و پوشش کاملا از بین میرود و بنابراین، پوشش نهایی هیچ مشخصه نانوساختاری مرتبط با پودر اولیه نشان نخواهد داد. به منظور رفع این مشکل، کنترل دقیق دمای ذرات در جت پاشش حرارتی، امری ضروری است. در این پژوهش بهینهسازی شرایط پاشش به عنوان هدف اصلی انتخاب شد. بهطوری که این محققان با طراحی و بهینهسازی پارامترهای مختلف پاشش توانستند به پوششی با کیفیت بسیار مطلوب دست پیدا کنند.
مهندس رضا قاسمی، دانشجوی دکتری رشته مهندسی مواد دانشگاه صنعتی مالک اشتر، در مورد این تحقیقات گفت: « در این پژوهش زیرلایههایی از جنس سوپرآلیاژ پایه نیکل (اینکونل ۷۳۸LC) انتخاب شد. دلیل انتخاب این نوع آلیاژ، شبیهسازی با شرایط صنعتی است به نحوی که از این آلیاژ در ساخت پرههای چرخشی توربین استفاده میشود. سپس دو نوع پوشش سد حرارتی متداول و نانوساختار بر روی زیرلایه پوشیده شده با آستری NiCrAlY به کمک فرایند پاشش پلاسمایی اتمسفری (APS) رسوب داده شد.
در فرایند پاشش پلاسمایی ترکیبی از گازهای آرگون و هیدروژن بهعنوان گاز کار برای تشکیل پلاسما به کار گرفته شد. از گاز آرگون به منظور تثبیت قوس در نازل و از گاز هیدروژن به منظور افزایش آنتالپی و ایجاد دمای بالاتر پلاسما استفاده شد. همچنین برای انتقال ذرات پودری از منبع تغذیهی پودر به مشعل پلاسما، از گاز آرگون به عنوان گاز حامل استفاده شد. مشخصهیابی ریزساختاری و فازی نمونهها به کمک میکروسکوپ الکترونی روبشی گسیل میدانی (FESEM) و پراش سنج پرتو ایکس (XRD) انجام گرفت. سپس جهت ارزیابی خواص مکانیکی پوششها، تست نانوفرورونده و استحکام چسبندگی انجام گرفت.»
سختی، مدول الاستیک و استحکام چسبندگی سه پارامتر مهم در تعیین خواص مکانیکی پوششهای سد حرارتی در برآورد طول عمر آنها هستند. مقادیر سختی و مدول الاستیک به دست آمده از آزمون نانو فرورونده نشان داد که پوششهای YSZ نانو ساختار نسبت به پوششهای متداول دارای سختی و مدول الاستیک بیشتری هستند. تخلخلها و ریزترکها در ریزساختار تأثیر بهسزایی در سختی و مدول الاستیک اندازهگیری شده دارند. همچنین، وجود ذرات ذوب نشده به شدت مدول الاستیک پوششهای زیرکنیایی را تحت تأثیر قرار میدهد. با افزایش تخلخل، حفرات و ریزترکها در پوشش، سختی و مدول الاستیک کاهش مییابد. کاهش تخلخلها و ریزترکها در اثر استفاده از پودر نانوساختار آگلومره شده، باعث افزایش سختی پوششهای نانوساختار شده است.
همچنین در این تحقیق، مقدار استحکام چسبندگی برای پوششهای سد حرارتی YSZ متداول و نانوساختار پاشش پلاسمایی شده، برابر با ۶/۲۴ و MPa 12/38 به دست آمد این در حالتی است که استحکام پیوندی سرامیکهای پاشش پلاسمایی شده روی زیرلایههای فلزی در محدوده ۱۵ تا MPa 25 گزارش شده است. بنابراین، استحکام چسبندگی به دست آمده برای این دو پوشش مخصوصاٌ پوشش نانوساختار بسیار مطلوب بوده است. این امر نشان دهنده انتخاب صحیح پارامترهای فرایند پاشش پلاسمایی است.
در پوششهای سد حرارتی متداول ترکها تا مرز اسپلتها بدون هیچ مانعی گسترش مییابند. در صورتی که در پوششهای نانوساختار به واسطه ریزساختاری دوگانه رشد ترک به وسیله ذرات ذوب نشده و یا به طور جزئی ذوب شده و همچنین حفرات میان ذرات ذوب نشده محدود میشود و به موجب آن استحکام پیوندی پوشش افزایش مییابد.»
ایشان با اشاره به کاربرد این طرح در صنایع ادامه داد: « یکی از کاربردهای پوششهای سد حرارتی در موتورهای توربینی است. در موتورهای توربینی گازی، جهت بهبود راندمان احتراق موتور و کاهش نشر گازهای گلخانهای، به دماهای ورودی بالای توربین احتیاج است. این نیازمندی میتواند با بهکارگیری تکنیکهای خنکسازی غیر اقتصادی و یا بهکارگیری پوششهای سد حرارتی نانوساختار (دارای هدایت حرارتی کمتری نسبت به پوششهای متداول هستند) مرتفع گردد. بنابراین استفاده از پوششهای سد حرارتی نانوساختار باعث افزایش راندمان (صرفهجویی اقتصادی) و کاهش آلودگی هوا خواهد داشت.»
قاسمی در مورد ادامه این تحقیقات نیز افزود: « پوششهای سد حرارتی نانوساختار بهوسیلهی فرایندهای متنوعی رسوبدهی میشود اما فرایند پاشش پلاسمایی پیش ماده محلول (SPPS) یک فرایند نسبتا جدیدی است که تا کنون فقط در مراکز دانشگاهی به آن پرداخته شده است. از مزایای مهم این فرایند حذف مرحله تولید منبع تغذیه پودری است که میتواند کاهش هزینههای تولید را در پی داشته باشد.»
نتایج این کار تحقیقاتی که بهوسیلهی مهندس رضا قاسمی (دانشجوی دکتری رشته مهندسی مواد دانشگاه صنعتی مالک اشتر)، دکتر رضا شجاعرضوی، دکتر رضا مظفرینیا (دانشیاران دانشکده مهندسی مواد دانشگاه صنعتی مالک اشتر) و حسین جمالی (دانشجوی دکتری رشته مهندسی مواد دانشگاه صنعتی مالک اشتر) صورت گرفته است، در مجله Ceramics International (جلد ۳۹، شماره ۸، دسامبر ۲۰۱۳، صفحات ۸۸۰۵-۸۸۱۳) منتشرشده است.